[EXCLUSIF] Contrairement aux idées reçues, l’informatique industrielle (OT) a une histoire aussi longue que l’informatique des bureaux (IT). Pour rappel, les premiers automates programmables ont été déployés dans les usines dès les années 1980. Les mots protocoles, système d’exploitation, supervision, etc., y sont couramment employés. La récente convergence OT-IT ouvre des perspectives jusque-là insoupçonnées.
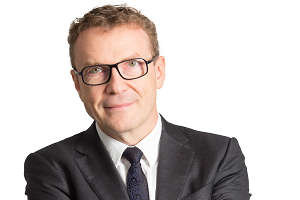
Michel Huy, directeur Information Solution de Rockwell Automation Europe
La jonction entre l’ERP1 et le MES2, par exemple, autorise une gestion plus fine des ressources humaines, des outils de production et des finances avec une vision à 360°, depuis les données brutes collectées par les capteurs jusqu’au lancement automatique d’une fabrication en fonction des prises de commande, une opération réalisée en temps quasi réel. Cette description n’est pas une vue de l’esprit puisque des manufactures, de plus en plus nombreuses à travers le monde, adoptent cette organisation. Pour elles, l’industrie qualifiée de « future » n’est pas un concept.
Cette évolution, si impressionnante soit-elle, masque l’arrivée de l’intelligence artificielle dans les usines. Ici, les ruptures qui s’annoncent seront telles qu’on peut parler de véritable entrée dans la 4e révolution industrielle.
L’IA a la particularité d’enrichir de fonctions cognitives les automates et les robots, qui étaient dotés jusque-là de fonctions préprogrammées. Ces outils deviennent capables d’autonomie décisionnelle grâce, notamment, à leurs nouvelles capacités d’auto-apprentissage. Par exemple, quand un moteur électrique de machine vibre anormalement, l’opérateur sait empiriquement qu’en abaissant la vitesse de rotation, il allonge la durée de vie du moteur, le temps de le changer entre deux cycles de production, évitant ainsi une panne aux conséquences financières autrement plus importantes que son simple remplacement.
Les capteurs savent remonter une information anormale du moteur mais les logiciels qui gèrent la production ignorent s’il faut réduire la vitesse du moteur et, si oui, à combien de tours par minute. Un programme d’IA, lui, saura adapter cette vitesse en toute autonomie.
Une fois cette explication formulée, se pose aussitôt la question légitime de l’avenir des opérateurs. Ce sujet est généralement abordé de deux manières : la première, largement majoritaire, considère que les opérateurs seront purement et simplement remplacés par les machines ayant l’IA dans leur ADN ; la seconde, celle que je défends, est optimiste. Mes années passées au plus près des lignes de production ne font dire que l’intelligence artificielle doit être accueillie comme une opportunité par et pour les opérateurs.
Les dirigeants exclusivement soucieux d’abaisser le coût de production devraient essayer un autre raisonnement. Sachant qu’un opérateur passe 90% de son temps à renseigner et à piloter des machines, il lui en reste 10 pour mettre en valeur ses savoir-faire, notamment dans l’amélioration des procédés de fabrication, souvent par petites touches incrémentales. Imaginons un opérateur libéré de 70% de tâches sans réelle valeur ajoutée : ses compétences associées à sa connaissance intime de l’atelier en feront aussitôt un hussard de l’entreprise. Et si l’intelligence artificielle venait à prendre une mauvaise décision, ce n’est pas exclu, seul un opérateur épanoui aura l’audace de reprendre en main le pilotage des machines.
En oeuvrant ensemble, intelligence artificielle et opérateurs feront l’entreprise industrielle gagnante de demain. Car l’intelligence artificielle sans l’intelligence humaine restera moins performante.
1 – ERP : suite logicielle pour la gestion des fonctions supports (comptabilité, RH, etc.)
2 – MES : suite logicielle pour la planification et la gestion de la production.