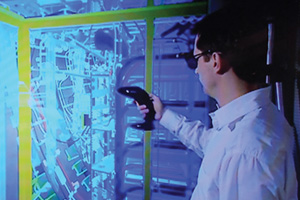
L’A350 XWB a été conçu à l’aide d’outils
d’analyse ergonomique réaliste.
Concevoir un produit de plus en plus complexe, avec une concurrence qui impose de raccourcir le cycle de développement et d’avoir recours massivement à la sous-traitance, tels ont été les enjeux du programme A350 pour Airbus.
Janvier 2003, Boeing dévoile son projet de long-courrier, le 7E7. L’avion sera renommé par la suite le 787 Dreamliner. Sur la promesse d’une baisse radicale de la consommation de kérosène, ce long-courrier engrange rapidement les commandes par dizaines, puis par centaines. Face au succès de son concurrent, Airbus pense un temps moderniser son A330, mais, à la mi-2006, le constructeur européen prend conscience qu’un A330 modernisé ne parviendra pas à rivaliser avec le Dreamliner… Décision est prise de concevoir un avion entièrement nouveau, l’A350 XWB. Les premiers vols d’essais se déroulent mi-2013, les premières livraisons sont prévues fin 2014. C’est donc avec trois ans (et près de 450 commandes !) de retard sur le Boeing 787 qu’Airbus lance un programme crucial pour son avenir. L’avionneur européen doit s’appuyer sur des technologies de rupture, notamment un fuselage en carbone, et le faire le plus rapidement possible pour ne pas laisser le 787 s’emparer seul du marché. « L’enjeu industriel de l’A350 est fort, résume Pierre Panfili, responsable du PLM et de la maquette numérique de l’A350. L’industrie aéronautique travaille sur des cycles très longs, avec des produits qui vivent vingt à trente ans. On a sécurisé notre entrée de gamme avec l’A320 Neo, on est en bonne position sur l’A380. Donc, si on réussit l’A350, on assure notre avenir sur quinze à vingt ans. » Pour raccourcir ses cycles de développement produit et lancer plus rapidement la production de ses nouveaux appareils, l’industrie aéronautique reprend de plus en plus un modèle proche de celui du secteur automobile. « Le schéma industriel de l’A350 est relativement classique et il évolue sur le modèle de celui de l’automobile. On fait de plus en plus appel à la sous-traitance. L’intégralité des systèmes électriques de l’A350 est sous-traitée, de même que la quasi-totalité des équipements et certaines parties de la structure de l’avion, reconnaît Pierre Panfili. Mais, en tant qu’architecte et responsable du produit, on en maîtrise la conception et, en termes de certifications, c’est bien Airbus qui s’engage sur les performances. » Le nombre d’intervenants dans la production de l’avion augmente, mais aussi le nombre d’ingénieurs qui participent à sa conception dans une approche de codesign désormais généralisée. Sur le programme A350, la part de la sous-traitance atteint 80 %, y compris sur le volet études. Une approche qui a une conséquence directe sur les échanges de données, comme le souligne Pierre Panfili : « Nous nous appuyons sur une centaine de fournisseurs de premier niveau qui, eux-mêmes, sous-traitent. Cela représente des échanges à n’en plus finir. Ce qui signifie que si on n’optait pas pour une maquette numérique centrale, la maîtrise de la configuration de l’appareil allait tourner au cauchemar. »
300 partenaires, 10 000 utilisateurs
Pour faire travailler simultanément plus de 7 200 ingénieurs sur l’avion, une seule solution possible, une maquette numérique unique. Tirant les conséquences des problèmes rencontrés lors de la conception de l’A380, entre autres la compatibilité entre les outils utilisés par ses différents sites industriels, qui avaient entraîné des complications au montage, Airbus a instauré Catia V5 de Dassault Systèmes comme outil de conception standard pour son bureau d’études interne comme pour ses partenaires. PTC Windchill est la solution de gestion des données PLM (gestion du cycle de vie du produit) et Dassault Systèmes Enovia héberge la maquette numérique de l’appareil. La décision est prise en 2006, mais le déploiement informatique est bouclé en 2008. Airbus a notamment poussé l’éditeur français à adapter son logiciel pour Microsoft Windows et à optimiser ses performances tout en acceptant un grand nombre d’utilisateurs. « La plate-forme devait être capable de gérer la confidentialité des données tout en étant ouverte simultanément aux 200 à 300 partenaires. Chaque jour, 4 000 des 10 000 utilisateurs de Catia V5 accèdent quotidiennement à la maquette numérique, avec une maquette mise à jour chaque heure. 85 % d’entre eux sont des utilisateurs hors Airbus. » Dassault Systèmes a accédé aux demandes de son puissant client et hâté le lancement la version 1.6 de sa plate-forme Enovia pour que celle-ci puisse être exploitée dans le cadre du programme A350. Le coup d’accélérateur apporté par la maquette numérique va être spectaculaire.
Ainsi, pour la conception de l’Airbus A320, lancée au début des années 1980, une boucle de conception complète, c’est-à-dire le temps mis pour transmettre une modification de conception à l’ensemble des fournisseurs, oscillait entre trois à cinq semaines. Lors du programme A380, après de gros efforts et de lourds investissements, Airbus est parvenu à ramener ce délai entre un et deux jours. Pour l’A350, celui-ci est inférieur à une heure. En dépit du nombre très important d’intervenants, de la lourdeur des fichiers de conception, Airbus est parvenu à augmenter de manière radicale la vitesse d’échange des données entre ses ingénieurs et ses partenaires. « Les résultats sont là. Par rapport au cycle de développement de l’A330, on a gagné six mois nets. Or, en termes de complexité industrielle, l’A350 n’a absolument rien à voir avec un A330. Ce dernier était, en quelque sorte, un super A320. » L’A350 a été conçu plus rapidement, mais surtout les pièces élaborées virtuellement pour le prototype se sont avérées bien plus précises que par le passé. Airbus estime avoir éliminé 80 % des retours de pièces au moment de l’assemblage du MSN 1, le premier exemplaire de l’A350. C’est sept fois moins de problèmes que pour l’A380. Une performance meilleure qu’attendue et qui a permis de réaliser la mise au point de l’appareil bien plus rapidement que prévu. Reste à l’avionneur européen à réussir la montée en cadence de la supply chain et de la chaîne de production de l’A350. L’avion vole, le carnet de commandes est plein, Toulouse a maintenant 814 appareils à livrer auprès de trente-neuf compagnies aériennes.
Photo : Airbus
Cet article est extrait du n°7 d’Alliancy, le mag